Small Room, Big Impact: Upgrade Your Mechanical/Electrical Space
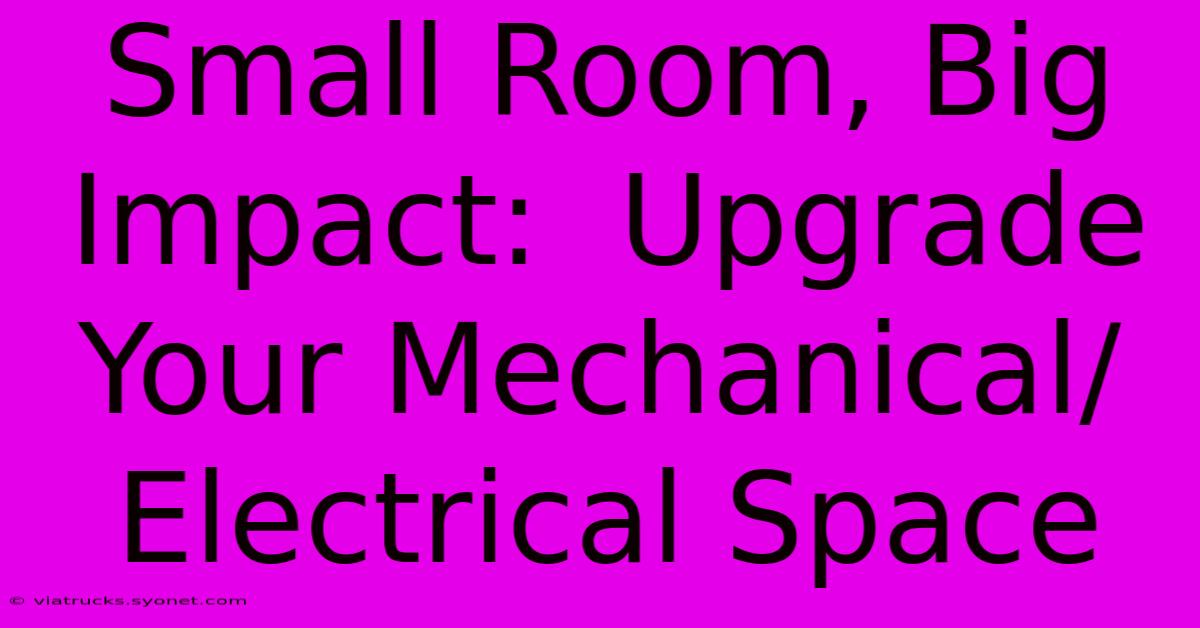
Table of Contents
Small Room, Big Impact: Upgrade Your Mechanical/Electrical Space
Mechanical and electrical rooms—often tucked away and overlooked—are the unsung heroes of any building. These spaces house the critical systems that keep everything running smoothly, from heating and cooling to power distribution. While they might be small, their impact is enormous. A well-organized and efficiently functioning mechanical/electrical (M/E) room is crucial for optimal building performance, reduced energy costs, and improved safety. This article explores practical strategies for upgrading your small M/E room to maximize its potential.
Assessing Your Current Situation: A Room Audit
Before diving into upgrades, a thorough assessment is essential. Consider these key factors:
- Space Constraints: Measure the room's dimensions and identify any obstacles like pipes, conduits, or awkwardly placed equipment. Knowing your limitations will inform your upgrade choices.
- Existing Equipment: List all current mechanical and electrical equipment, noting its age, condition, and energy efficiency. Outdated or inefficient equipment is a prime target for upgrades.
- Wiring and Piping: Inspect the wiring and piping systems for damage, corrosion, or inadequate capacity. Addressing these issues proactively prevents future problems.
- Ventilation and Cooling: Check the adequacy of ventilation and cooling. Overheating can damage equipment and create safety hazards.
- Accessibility: Ensure sufficient space for maintenance and repairs. Proper aisle widths and clear pathways are critical for safe and efficient service.
- Safety Compliance: Verify compliance with all relevant safety regulations and codes.
Maximizing Space: Smart Organization and Layout
Small spaces demand clever solutions. Here's how to optimize your M/E room's layout:
Vertical Space Utilization:
- Wall-mounted racks: Utilize wall space for mounting equipment racks, freeing up valuable floor space.
- Multi-tiered shelving: Install sturdy shelving systems to store spare parts, tools, and documentation. Keep frequently used items easily accessible.
- Overhead storage: If ceiling height allows, consider overhead storage for less frequently used items.
Floor Space Optimization:
- Modular equipment: Choose compact, modular equipment designed to fit small spaces.
- Consolidated wiring: Use cable management systems to neatly organize and route wiring, improving airflow and preventing tangles.
- Space-saving equipment: Explore options for smaller, more efficient HVAC units, pumps, and other critical systems.
Key Upgrades for Enhanced Efficiency and Safety
Several strategic upgrades can dramatically improve your M/E room's performance:
Energy-Efficient Equipment:
- High-efficiency HVAC systems: Replacing outdated HVAC equipment with energy-efficient models significantly reduces energy consumption and operational costs. Consider variable-speed drives for improved control and efficiency.
- LED lighting: Switch to energy-efficient LED lighting to reduce energy use and improve illumination.
- Smart power monitoring: Implement a system for real-time monitoring of energy usage. This allows for better identification of potential energy waste and opportunities for optimization.
Improved Safety Measures:
- Proper grounding and bonding: Ensure proper grounding and bonding to prevent electrical hazards.
- Fire suppression system: Install a fire suppression system tailored to the specific risks in your M/E room.
- Emergency lighting: Provide adequate emergency lighting to ensure safe evacuation in case of a power outage.
- Clear signage and labeling: Use clear signage and labeling to identify equipment, circuits, and safety procedures.
Remote Monitoring and Control:
- Building Management Systems (BMS): Integrating a BMS allows for remote monitoring and control of various M/E systems. This enables proactive maintenance and optimization of building performance.
- Predictive Maintenance: Utilize data from the BMS to predict potential equipment failures and schedule maintenance proactively, minimizing downtime.
Ongoing Maintenance: The Key to Long-Term Success
Regular maintenance is crucial to maximizing the lifespan and efficiency of your M/E room's equipment and systems. Establish a preventative maintenance schedule and adhere to it diligently. This includes regular inspections, cleaning, and minor repairs to prevent costly breakdowns and ensure optimal performance.
By strategically upgrading your small mechanical/electrical room, you can achieve a significant impact on your building's overall efficiency, safety, and operational costs. Remember to prioritize safety, plan for future expansion, and invest in high-quality, energy-efficient equipment. The result will be a more reliable, efficient, and safer environment for years to come.
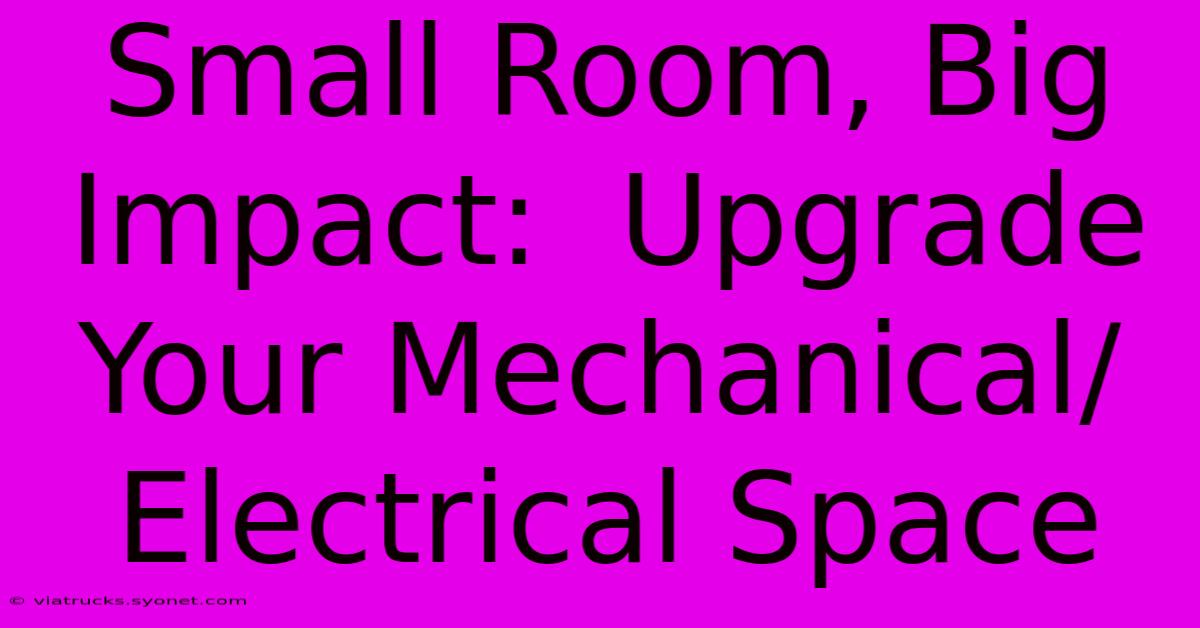
Thank you for visiting our website wich cover about Small Room, Big Impact: Upgrade Your Mechanical/Electrical Space. We hope the information provided has been useful to you. Feel free to contact us if you have any questions or need further assistance. See you next time and dont miss to bookmark.
Featured Posts
-
Decouverte A Epinay Reactions Des Habitants
Feb 09, 2025
-
Margarita Rosa De Franciscos Unexpected Secret To Benefit
Feb 09, 2025
-
Brownells 2028 Presidential Run
Feb 09, 2025
-
Confused By Cats Cradle This Will Make It Clear
Feb 09, 2025
-
Who Can You Trust The Traitors Season 3 Predictions
Feb 09, 2025