From Chaos To Calm: Taming The Mechanical/Electrical Room Beast
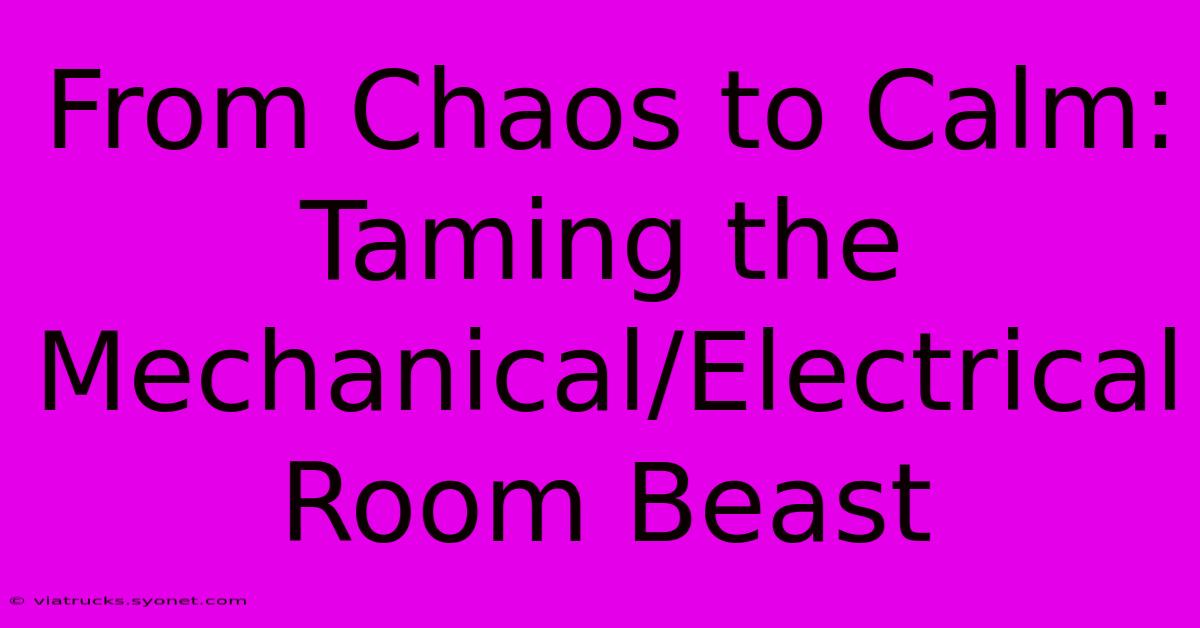
Table of Contents
From Chaos to Calm: Taming the Mechanical/Electrical Room Beast
Mechanical and electrical (M/E) rooms are the unsung heroes of any building. They house the critical systems keeping everything running smoothly – HVAC, plumbing, power distribution, fire safety – the list goes on. But these rooms can quickly descend into chaos if not properly managed. This article will guide you through strategies to transform your M/E room from a tangled mess into an organized, efficient, and safe space.
Understanding the M/E Room Monster: Identifying the Problems
Before tackling the beast, we need to understand its nature. Common issues plaguing M/E rooms include:
- Poor Organization: Lack of labeling, haphazard cable routing, and unsorted equipment leads to confusion and delays during maintenance or repairs.
- Safety Hazards: Exposed wiring, tripping hazards, inadequate lighting, and lack of proper safety signage create a dangerous working environment.
- Inefficient Space Utilization: Poor planning and lack of space optimization lead to wasted space and difficulties in accessing equipment.
- Lack of Documentation: Insufficient or outdated documentation makes troubleshooting and maintenance a nightmare.
- Temperature and Humidity Issues: Extreme temperatures or humidity can damage equipment and reduce its lifespan.
Taming the Beast: Practical Steps to a More Organized M/E Room
Transforming your M/E room requires a systematic approach. Follow these steps to regain control:
1. Conduct a Thorough Assessment: The First Step to Organization
Begin with a comprehensive audit. Document everything:
- Equipment Inventory: Create a detailed list of all equipment, including model numbers, serial numbers, and maintenance schedules.
- Wiring and Piping Diagrams: Update existing diagrams or create new ones if necessary. Clearly label all wires and pipes.
- Safety Hazards: Identify and document all potential safety hazards.
- Space Utilization Analysis: Assess how space is currently used and identify areas for improvement.
2. Declutter and Organize: The Power of a Clean Slate
Once you've assessed the situation, it's time to declutter. Remove any unnecessary equipment, materials, or debris. Organize remaining items using these strategies:
- Labeling System: Implement a clear and consistent labeling system for all equipment, wires, and pipes.
- Cable Management: Use cable ties, trays, and conduits to neatly organize cables and prevent tangling.
- Equipment Racking: Install equipment racks to consolidate equipment and improve accessibility.
- Storage Solutions: Utilize shelving units and cabinets to store spare parts, tools, and documentation.
3. Prioritize Safety: Protecting People and Equipment
Safety is paramount. Implement these safety measures:
- Proper Lighting: Ensure adequate lighting throughout the room.
- Safety Signage: Install clear and visible safety signage.
- Emergency Shut-off Switches: Ensure easy access to emergency shut-off switches.
- Fire Suppression System: Regularly inspect and maintain fire suppression systems.
- Personal Protective Equipment (PPE): Make sure appropriate PPE is readily available.
4. Implement a Preventative Maintenance Program: Proactive vs. Reactive
Regular preventative maintenance is key to preventing major issues and extending the lifespan of your equipment. Establish a schedule for regular inspections and maintenance tasks.
5. Documentation is Key: Maintaining Order and Efficiency
Keep your documentation updated. This includes:
- Equipment Manuals: Keep manuals readily accessible for all equipment.
- Maintenance Logs: Maintain detailed logs of all maintenance activities.
- As-Built Drawings: Update as-built drawings to reflect any changes to the M/E room.
Beyond the Room: The Broader Perspective
Maintaining a well-organized M/E room isn't just about aesthetics; it impacts the entire building's efficiency and safety. A well-maintained M/E room translates to:
- Reduced Downtime: Easier troubleshooting and maintenance means less downtime.
- Improved Energy Efficiency: Properly maintained equipment operates more efficiently, reducing energy consumption.
- Enhanced Safety: A safer environment for maintenance personnel.
- Increased Property Value: A well-maintained M/E room can increase the value of your property.
By following these steps, you can transform your M/E room from a chaotic mess into a well-organized, efficient, and safe space. Remember, the effort is an investment in the long-term health and efficiency of your entire building.
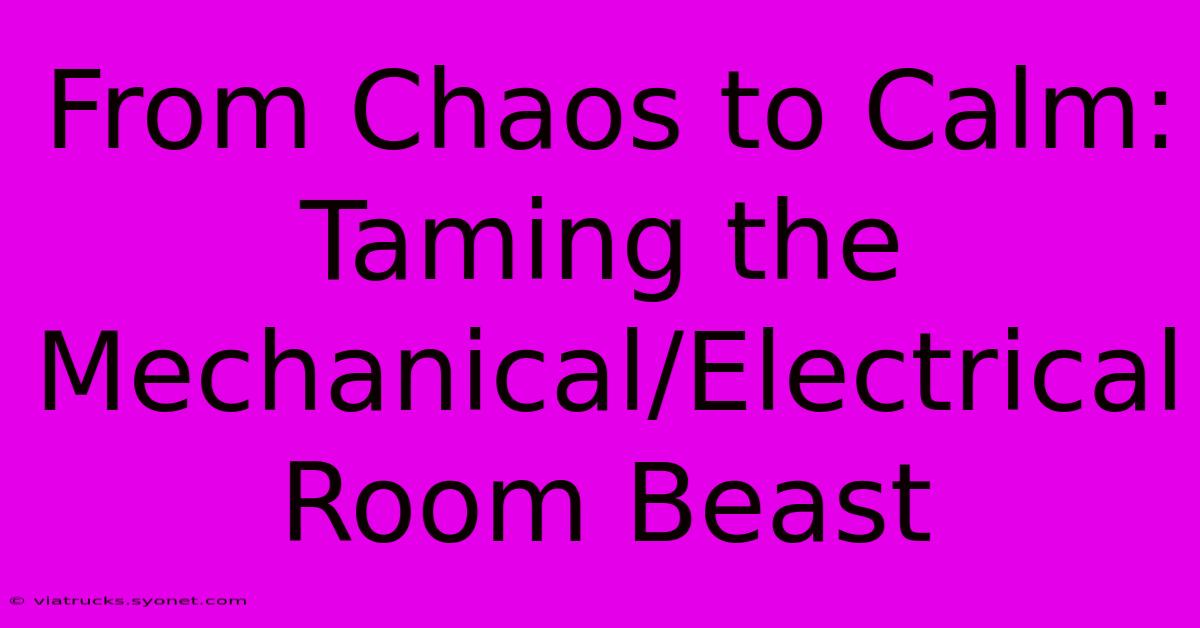
Thank you for visiting our website wich cover about From Chaos To Calm: Taming The Mechanical/Electrical Room Beast. We hope the information provided has been useful to you. Feel free to contact us if you have any questions or need further assistance. See you next time and dont miss to bookmark.
Featured Posts
-
Beyond The Flames The Hidden Power Of Avatar Fire And Ash
Feb 10, 2025
-
Super Bowl Lix Mvp Jalen Hurts
Feb 10, 2025
-
Nothing More Nothing Less The Secret To True Happiness
Feb 10, 2025
-
Beyond The Wiz Explore Shanice Williams Filmography
Feb 10, 2025
-
Shocking Truth About Maddox Batsons Age
Feb 10, 2025